Understanding UV Curable Ink: Revolutionizing the Printing Industry
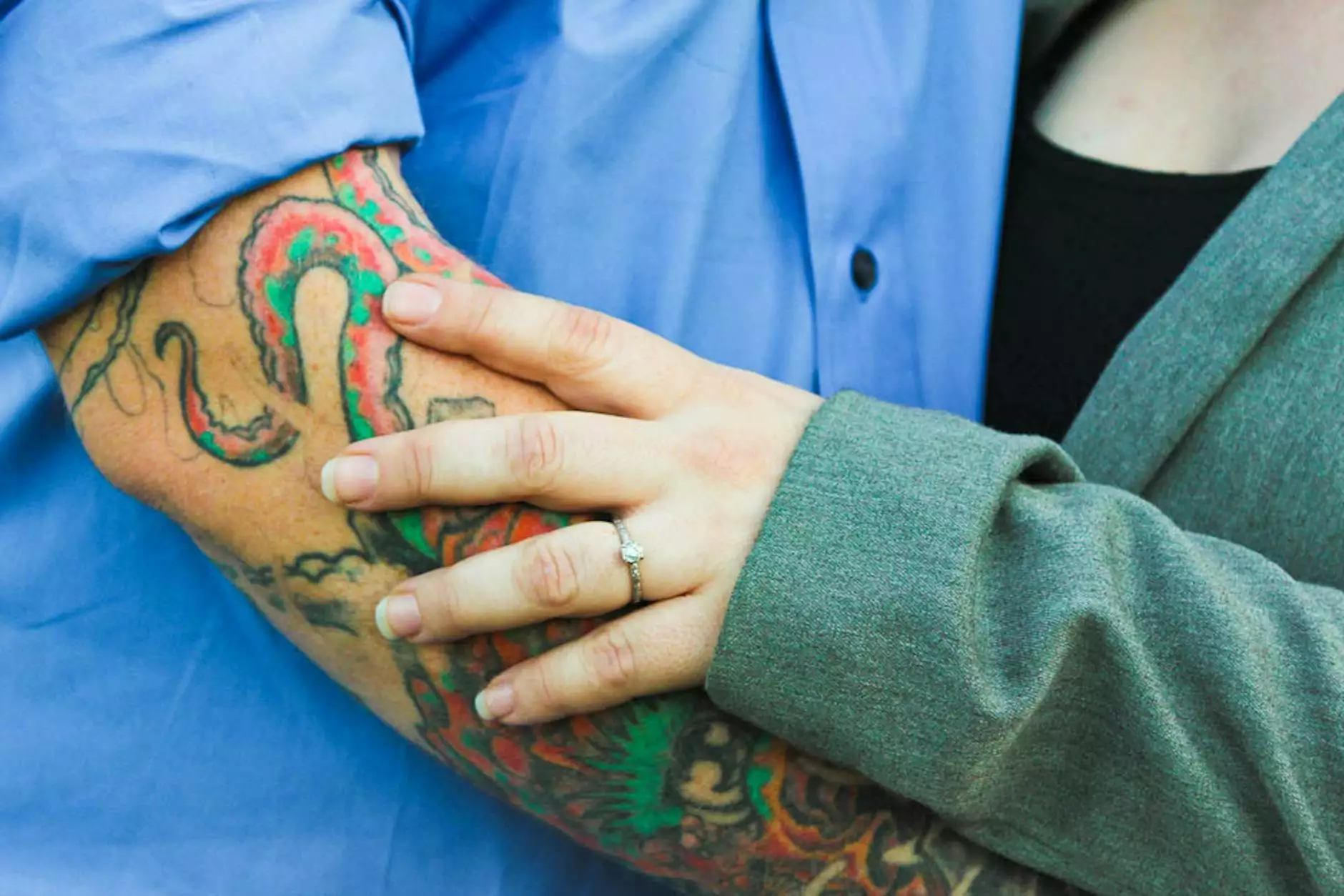
UV curable ink stands at the forefront of modern printing technology, offering unparalleled advantages over traditional inks. As businesses, including Boston Industrial Solutions, continue to innovate their printing services, understanding the profound impact of UV curable inks is essential for anyone involved in the printing industry.
What is UV Curable Ink?
UV curable ink is a type of ink that is cured, or solidified, using ultraviolet (UV) light. This process transforms the liquid ink into a solid form almost instantly upon exposure to UV light. The technology behind UV inks has been embraced due to its many benefits and applications.
How Does UV Curing Work?
The process of UV curing involves several key steps:
- Ink Application: The UV ink is applied to the substrate through various printing techniques such as screen printing, inkjet printing, or flexography.
- UV Exposure: Once the ink is applied, the substrate passes under a UV lamp, where the UV light triggers a chemical reaction in the ink. This reaction causes the ink to dry rapidly.
- Final Product: The result is a fully cured, durable finish that adheres strongly to the substrate.
Advantages of UV Curable Ink
UV curable inks offer a plethora of advantages over traditional inks:
1. Fast Drying Time
One of the key benefits of UV curable ink is its remarkably fast drying time. This rapid curing allows for quicker production times and immediate handling.
2. High Durability
UV inks are known for their exceptional durability. Once cured, they can resist scratches, chemical spills, and UV exposure, ensuring the longevity of printed materials.
3. Vibrant Colors and High Resolution
UV curable inks deliver vibrant colors and excellent image quality. The rapid curing prevents ink spreading, allowing for highly detailed and high-resolution prints.
4. Environmental Benefits
These inks are often more environmentally friendly compared to solvent-based inks. UV curable inks emit low levels of volatile organic compounds (VOCs), making them a safer choice for both workers and the environment.
5. Versatile Substrate Compatibility
UV curable inks can be used on a wide variety of substrates, including plastics, metals, glass, and paper. This versatility makes them suitable for many different applications.
Applications of UV Curable Ink
The applications of UV curable ink are vast and span across numerous industries:
1. Packaging
In the packaging industry, UV inks are utilized for their quick drying capabilities, allowing for faster production cycles and improved shelf appeal with vibrant colors.
2. Commercial Printing
UV curable inks are widely used in commercial printing for items such as business cards, brochures, and promotional materials, enabling high-quality outputs.
3. Signage and Displays
For outdoor signage, UV inks offer excellent weather resistance, ensuring that printed materials maintain their appearance for extended periods despite exposure to the elements.
4. Labels
Label printing often benefits from UV inks as they can produce intricate designs with high clarity, which is essential for brand recognition.
Why Boston Industrial Solutions Chooses UV Curable Ink
At Boston Industrial Solutions, the choice to employ UV curable ink reflects our commitment to providing top-tier printing services. We recognize the crucial advantages this technology brings to our operations, allowing us to serve our clients with:
- Uncompromised Quality: Our use of UV inks ensures that every print job meets the high standards expected by our clientele.
- Efficiency: The fast curing process enables us to keep production timelines tight while delivering on time.
- Innovation: We are dedicated to staying ahead in the industry by adopting the latest technologies, including UV printing.
Challenges and Considerations for UV Curable Inks
Despite their numerous advantages, UV curable inks come with some challenges that businesses should be aware of:
1. Equipment Costs
Investing in UV printing equipment can be substantial. The initial outlay for UV curing systems may pose a challenge for small businesses.
2. Technical Expertise
Operating UV printing systems requires specific technical knowledge to ensure optimal performance and quality control.
3. Limited Flexibility Post-Curing
Once cured, UV inks are more difficult to manipulate or modify. This rigidity must be considered during the design phase.
The Future of UV Curable Ink in Printing
The future of UV curable ink looks promising, as innovations continue to emerge. The following advancements are projected to shape its trajectory:
1. Enhanced Formulations
Ongoing research is leading to the development of more advanced UV ink formulations which provide even greater durability and a broader range of applications.
2. Sustainable Practices
With increasing demand for sustainable printing solutions, manufacturers are focusing on developing eco-friendly UV inks that further reduce environmental impact.
3. Technological Integration
As printing technology evolves, the integration of UV inks with digital printing technologies is likely to grow, resulting in higher efficiency and expanded capabilities.
Conclusion
In summary, UV curable ink presents transformative possibilities for the printing industry, encompassing remarkable advantages such as rapid drying, exceptional durability, and vibrant output quality. As companies like Boston Industrial Solutions adopt these advanced technologies, the future of printing services is clearly aligned with the potential of UV curing technology. Whether you are in packaging, commercial, or signage printing, understanding the role of UV curable inks can provide a competitive edge in delivering superior quality products.
As we continue to explore and innovate within the realm of printing, the potential applications and efficiencies of UV curable ink will no doubt pave the way for a brighter, more vibrant future in the printing industry.