The Future of Automotive CNC Machining: Revolutionizing Metal Fabrication
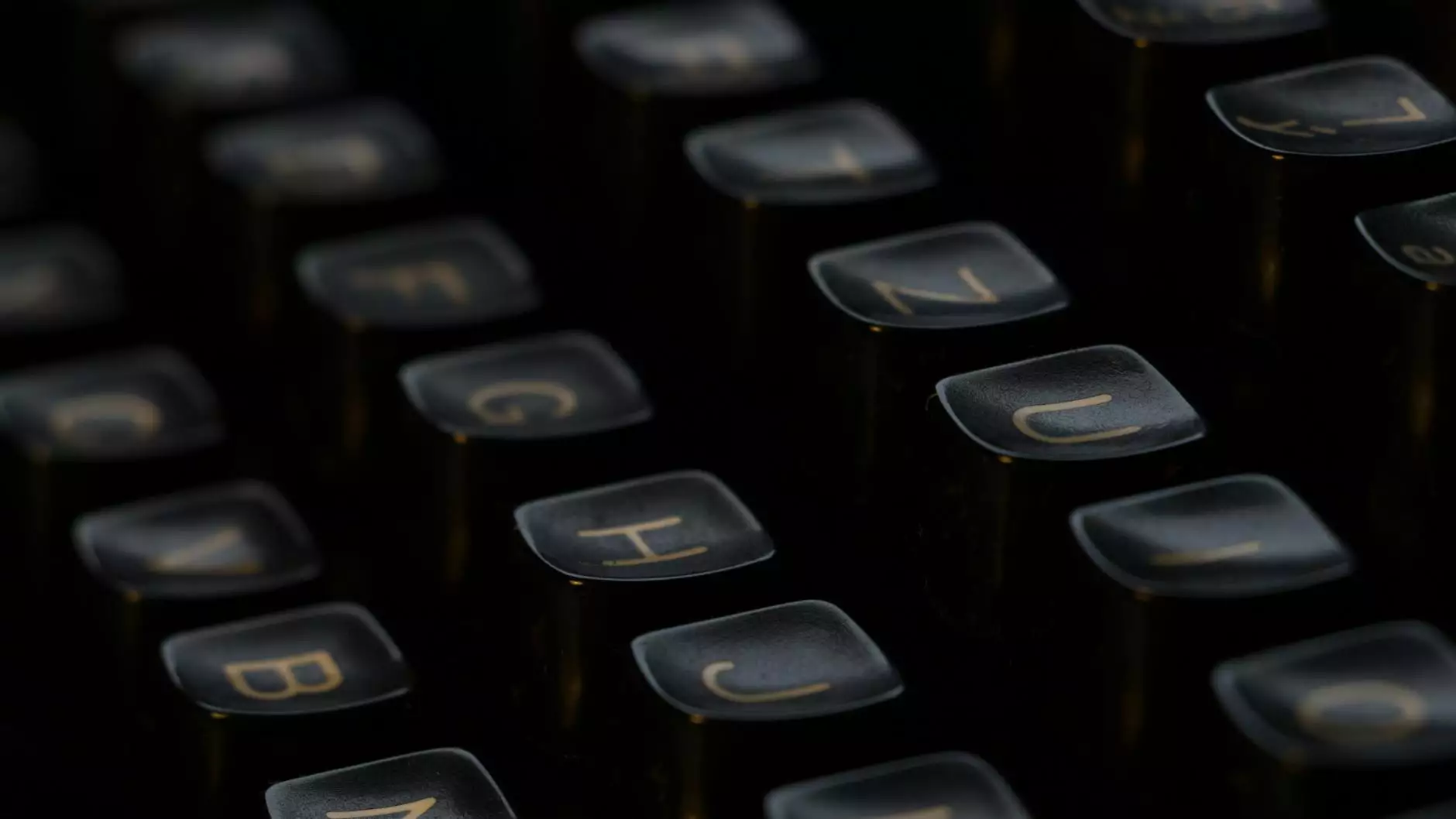
In the rapidly evolving world of automotive manufacturing, automotive CNC machining stands out as a pivotal technology that is reshaping metal fabrication. With its precision, speed, and efficiency, CNC (Computer Numerical Control) machining is not merely a method; it is an art form that enhances the production capabilities of automotive components. In this comprehensive article, we delve into the intricacies of automotive CNC machining, its applications, advantages, and its future in the industry.
Understanding Automotive CNC Machining
Automotive CNC machining is a manufacturing process that uses computerized controls to operate machine tools. This technology enables the production of intricate parts and components with high accuracy and repeatability. The process involves converting a digital design into a physical object through various techniques, including milling, turning, and drilling, using cutting tools under precise control.
Key Components of the CNC Machining Process
- CNC Programming: This is the initial stage where a technician writes a program that contains the specifications of the part to be manufactured.
- Machine Setup: The CNC machine is set up with the correct tools and fixtures based on the program requirements.
- Execution: Once everything is set, the CNC machine executes the program, transforming raw materials into finished components.
- Quality Control: Throughout the machining process, quality checks are performed to ensure dimensional accuracy and surface finish.
Advantages of Automotive CNC Machining
The adoption of automotive CNC machining offers numerous advantages that enhance manufacturing processes:
1. Precision and Accuracy
One of the foremost advantages of CNC machining is its unmatched precision. The computerized control system allows for tolerances within microns, which is critical in the automotive industry where even slight deviations can lead to significant performance issues.
2. Increased Efficiency
Automotive CNC machining significantly reduces production time. Once the initial setup and programming are completed, components can be manufactured in rapid succession with minimal human intervention, reducing labor costs and increasing throughput.
3. Flexibility in Design
With CNC machining, manufacturers can easily adapt to changes in design specifications. Quick alterations can be made to the program to accommodate new designs or modifications without the need for extensive retooling.
4. Material Versatility
CNC machining can be applied to a wide range of materials commonly used in the automotive industry, including metals like aluminum, steel, and titanium, as well as plastics and composites. This versatility expands the possibilities for innovative component design.
5. Enhanced Safety
The automation of machining processes reduces the potential for human error, thus enhancing workplace safety. Operators oversee the machines rather than manually controlling them, minimizing risk factors associated with traditional machining methods.
Applications of Automotive CNC Machining
The applications of automotive CNC machining are diverse, ranging from prototyping to full-scale production of critical automotive components. Some of the key applications include:
1. Engine Components
High-performance engines often consist of precisely machined components such as cylinder heads, intake manifolds, and valve covers. CNC machining ensures that these parts fit together seamlessly, enhancing engine performance and reliability.
2. Transmission Parts
The transmission system is vital for effective power delivery in vehicles. CNC machined parts such as gears and housings are crucial for their performance and durability. The precision of CNC machining minimizes lost power during transmission.
3. Chassis and Structural Components
Modern automotive design increasingly relies on lightweight materials for chassis construction. CNC machining enables the manufacturing of complex shapes and structures that maintain strength while reducing weight, contributing to improved fuel efficiency.
4. Customization and Aftermarket Parts
CNC machining opens doors for custom automotive parts, catering to enthusiasts looking to enhance their vehicles. From specialized brackets to custom intake systems, the possibilities are virtually limitless.
The Role of Technology in Automotive CNC Machining
The technological advancements in CNC machinery and software directly influence the efficiency and effectiveness of the machining process. Here are some recent innovations:
1. Advanced Software Solutions
The evolution of CAD (Computer-Aided Design) and CAM (Computer-Aided Manufacturing) software has revolutionized how design and manufacturing processes interconnect. Enhanced simulation capabilities within these software systems allow manufacturers to foresee mistakes and optimize machining processes before physical production begins.
2. Multi-axis Machining
Multi-axis CNC machines, allowing simultaneous movement along multiple axes, provide unparalleled flexibility and the ability to create complex geometries. This advancement minimizes the need for multiple setups, reducing lead times and improving overall efficiency.
3. Automation and Robotics
Integrating robotics into CNC machining not only streamlines production but also enhances precision and consistency. Robotic arms can handle loading and unloading while the CNC machines operate, freeing skilled workers to focus on value-added tasks.
Challenges in Automotive CNC Machining
Despite the advantages, automotive CNC machining is not without challenges. Addressing these is crucial for maintaining efficiency:
1. High Initial Investment
The cost of CNC machinery and software can be significant, especially for small-to-medium enterprises (SMEs). However, considering the return on investment (ROI) through increased productivity and precision often justifies the initial expenditure.
2. Skilled Workforce Requirement
Although CNC machines operate automatically, they require skilled operators for programming, setup, and monitoring. Investing in workforce training is essential to ensure operators possess the necessary skills to maximize the capabilities of CNC technology.
3. Maintenance and Repair Costs
Like any sophisticated machinery, CNC machines require regular maintenance to operate efficiently. Establishing a proactive maintenance schedule can mitigate unexpected downtime and repair costs.
The Future of Automotive CNC Machining
The future of automotive CNC machining is poised for growth and innovation. As manufacturers seek to optimize production processes, advancements such as AI-driven systems, IoT integration for smarter manufacturing, and additive manufacturing techniques will likely play pivotal roles. Here’s what to expect:
1. Intelligent Manufacturing Systems
The incorporation of artificial intelligence (AI) enables CNC machines to analyze operational data in real-time, predict maintenance needs, and optimize cutting paths, enhancing overall productivity.
2. Sustainability Practices
With growing emphasis on sustainability, automotive manufacturers are exploring ways to minimize waste in the machining process. Efficient material usage and recycling strategies will be critical in meeting environmentally-friendly production targets.
3. Greater Collaboration Across Industries
The automotive industry will continue to see collaboration with tech firms to integrate cutting-edge technologies, further enhancing the capabilities of CNC machining. Innovations from industries such as aerospace and robotics will likely influence automotive machining practices.
Conclusion
In conclusion, automotive CNC machining represents a significant leap in manufacturing technology, bringing numerous advantages to the automotive industry. Its precision, efficiency, and adaptability make it a cornerstone of modern metal fabrication, providing the ability to produce high-quality components that meet the evolving demands of today’s automotive landscape. By embracing the future advancements in this field, businesses like Deep Mould can position themselves at the forefront of the industry, paving the way for continued growth and innovation.
As we move forward, it is crucial for manufacturers to invest in technology, train skilled labor, and adapt to the advancements in CNC machining to harness its full potential. The journey is just beginning, and the possibilities are endless.